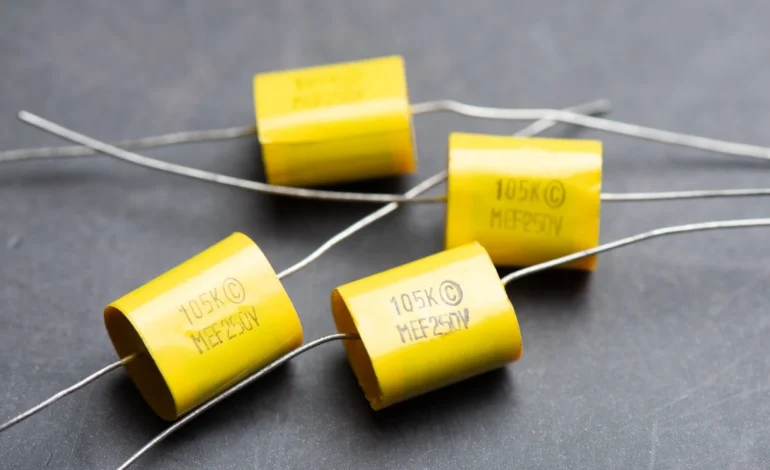
How Accurate Measurements Enhance Film Capacitor Production
In the film capacitor industry, precision isn’t just important—it’s non-negotiable. From optimizing the electrical properties of materials to ensuring consistent production quality, accurate measurements play a pivotal role at every stage. Whether it’s determining sheet resistance, conductance, or the thickness of conductive layers, these measurements directly influence the performance and reliability of the final product.
What Is Measured in Film Capacitor Production?
Film capacitor manufacturing relies on precise measurements of key material properties to ensure that each capacitor meets design specifications. The most critical parameters include:
Sheet resistance
Reflects the resistance of a thin conductive layer, essential for predicting how the material will perform in an electrical circuit.
Sheet conductance
Indicates how efficiently the material conducts electrical current, the inverse of sheet resistance.
Thickness
Determines the durability and performance of both the dielectric layer and conductive materials.
These properties are directly tied to the capacitor’s ability to store energy, maintain stability under varying conditions, and provide long-term reliability.
Materials Involved in Film Capacitor Manufacturing
Accurate capacitor measurement systems must account for the specific properties and challenges associated with the materials used in film capacitors. This includes addressing variations in material composition and performance requirements to ensure consistent results across different applications. These include:
Electrode Materials:
● Aluminum and aluminum alloys
● Zinc and zinc alloys
Dielectric Types:
● Polypropylene (PP), commonly known as Treofan
● Polyester (PET), such as Hostaphan or Mylar
● Polyethylene naphthalate (PEN), e.g., Kaladex
● Polyphenylene sulfide (PPS), like Torelina
● Polytetrafluoroethylene (PTFE), better known as Teflon
● Polystyrene (PS), such as Styroflex
● Polycarbonate (PC), also called Makrofol
Each material comes with its own set of characteristics, requiring precise measurement to ensure optimal electrical performance.
How Accurate Measurements Improve Production
The production process for film capacitors involves several critical stages where accurate measurements can make all the difference:
1. Research and Development
During R&D, manufacturers experiment with different conductive layer “recipes” to achieve the desired electrical properties. Accurate measurement of sheet resistance and conductance ensures that each iteration aligns with the target specifications, accelerating development.
2. Material Production
In the production phase, electrode materials must meet strict thickness requirements. Whether the metal is being rolled to achieve the desired thickness or deposited onto a dielectric layer, precise, real-time measurements ensure consistency. For example:
● When rolling foils, sensors provide feedback at each step to maintain uniform thickness.
● During vacuum deposition, inline sensors monitor the thickness of the evaporated material to ensure proper layer formation.
3. Quality Control Before Slitting
Before the “mother roll” of material is slit into smaller widths, manufacturers must confirm that it meets all specifications. Measurements of sheet resistance and thickness ensure uniformity across the roll, minimizing waste and maximizing efficiency.
4. Pre-Capacitor Assembly
In the final stages, materials are inspected once more to confirm that they meet the required electrical and physical properties. This step ensures that only high-quality materials proceed to the winding and assembly process.
Advantages of Advanced Measurement Systems in Film Capacitor Manufacturing
Traditional measurement methods, such as optical systems or four-point probes, have significant limitations. Advanced sensors provide several advantages that make them ideal for film capacitor production:
● Non-destructive testing – Measurements are taken without damaging the material, preserving its integrity.
● Inline compatibility – Sensors can measure materials in real time during production, providing instantaneous feedback.
● Ability to read through insulating layers – This feature allows for accurate measurements of metalized films without removing dielectric coatings.
● Real-time process inspection – Continuous monitoring ensures consistency and identifies issues immediately.
● Unaffected by texture or patterns – Measurements remain reliable even on materials with complex surface features.
Recommended Deployment Strategies
To get the most out of advanced measurement systems, strategic deployment is crucial. Here are some best practices for implementation:
Inline Monitoring During Production
Metal rolling – Use sensors at each stage of rolling to monitor thickness and adjust processes in real time.
Vacuum deposition – Place sensors inside the deposition chamber to measure the thickness of metalized layers immediately after application.
Quality Assurance
Cross-web monitoring – Deploy multiple sensors across the width of the material to ensure uniformity.
Downstream consistency – Use sensors to monitor materials after key production steps, ensuring they remain within tolerance.
Research and Development
For benchtop testing of new materials, advanced sensors provide precise measurements of sheet resistance and conductance, supporting rapid iteration and innovation.
Why Measurement Precision Matters
Precision in measurement directly impacts the quality and performance of film capacitors. By accurately measuring key parameters, manufacturers can:
● Optimize electrical performance – Achieve consistent capacitance, reliability, and energy storage.
● Reduce waste – Detect and address material inconsistencies early, minimizing rejected products.
● Increase efficiency – Real-time feedback shortens production cycles and accelerates troubleshooting.
● Enhance product reliability – Capacitors made with accurately measured materials are less prone to failure, even in demanding applications.
The Future of Film Capacitor Manufacturing
As the demand for high-performance capacitors continues to grow, accurate measurement systems will remain at the forefront of innovation. Advanced sensor technologies provide manufacturers with the tools they need to stay competitive, ensuring that every capacitor meets the highest standards of quality and reliability. By implementing precise measurement techniques, manufacturers can confidently produce capacitors that excel in performance, durability, and efficiency.